‘Enfys’ needed some fairly major maintenance and this had been in the planning for about a year. She had a busy 2018 sailing season with Bill Dowell- about twenty five separate trips and short voyages. But with concerns about the condition of her stern-tube he decided to carry out work over the winter 2018/2019.
She was brought by road to a yard in Pembroke Dock after mast was un-stepped and all heavy and loose gear was removed.

Chocked up and sheeted-over the first job was to unbolt and lift out her engine and associated gear including fuel tank. The inboard nuts of the two aftermost centreline ballast keel bolts are under the engine.

The centreboard lifting wire was disconnected and pivot bolt removed – here it is after just four seasons’ use showing the wasting caused by the fretting and movement of the ‘plate in use. This is an M24 bolt.
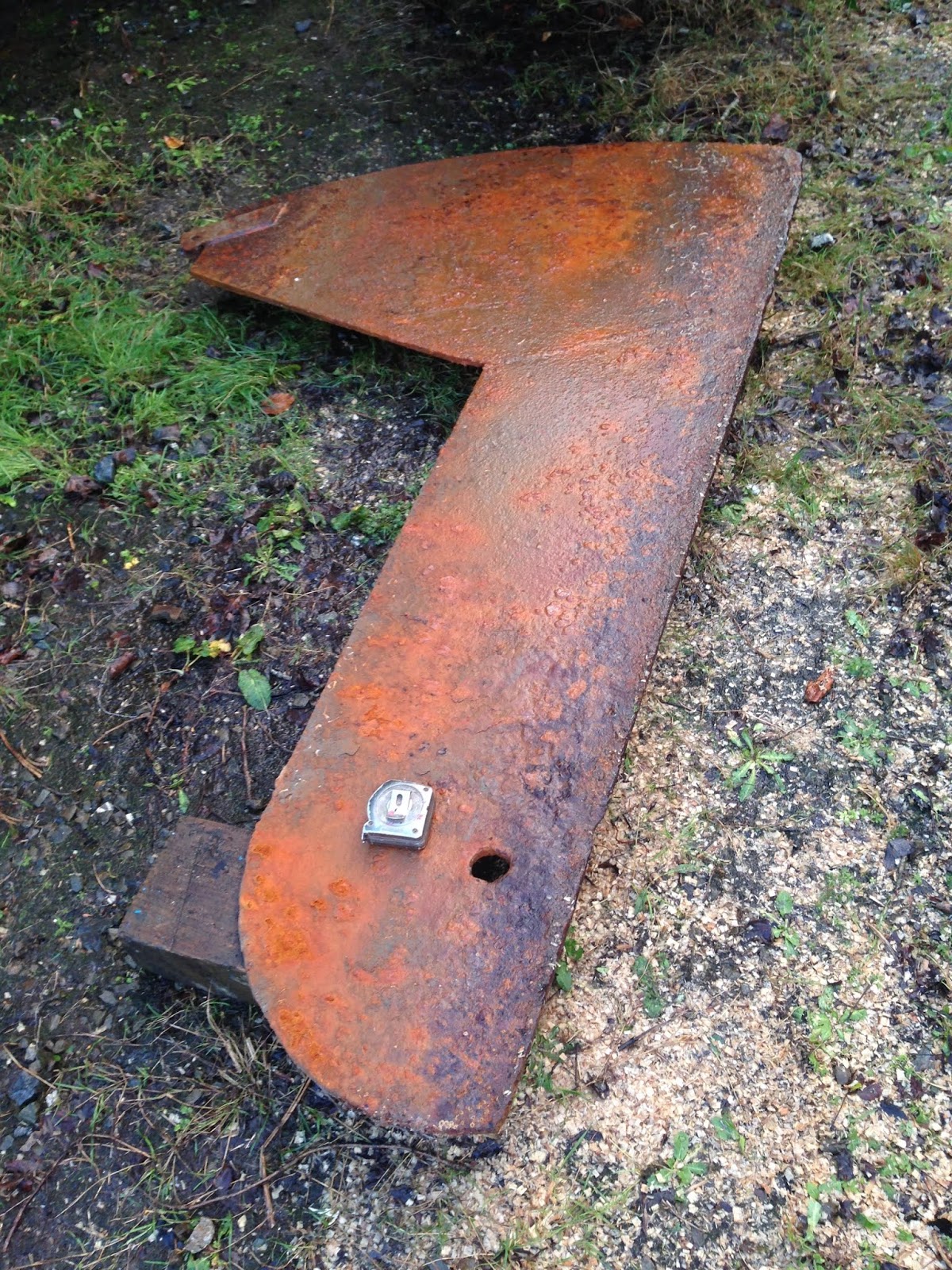
The yacht was lifted off her centreplate to extract it…
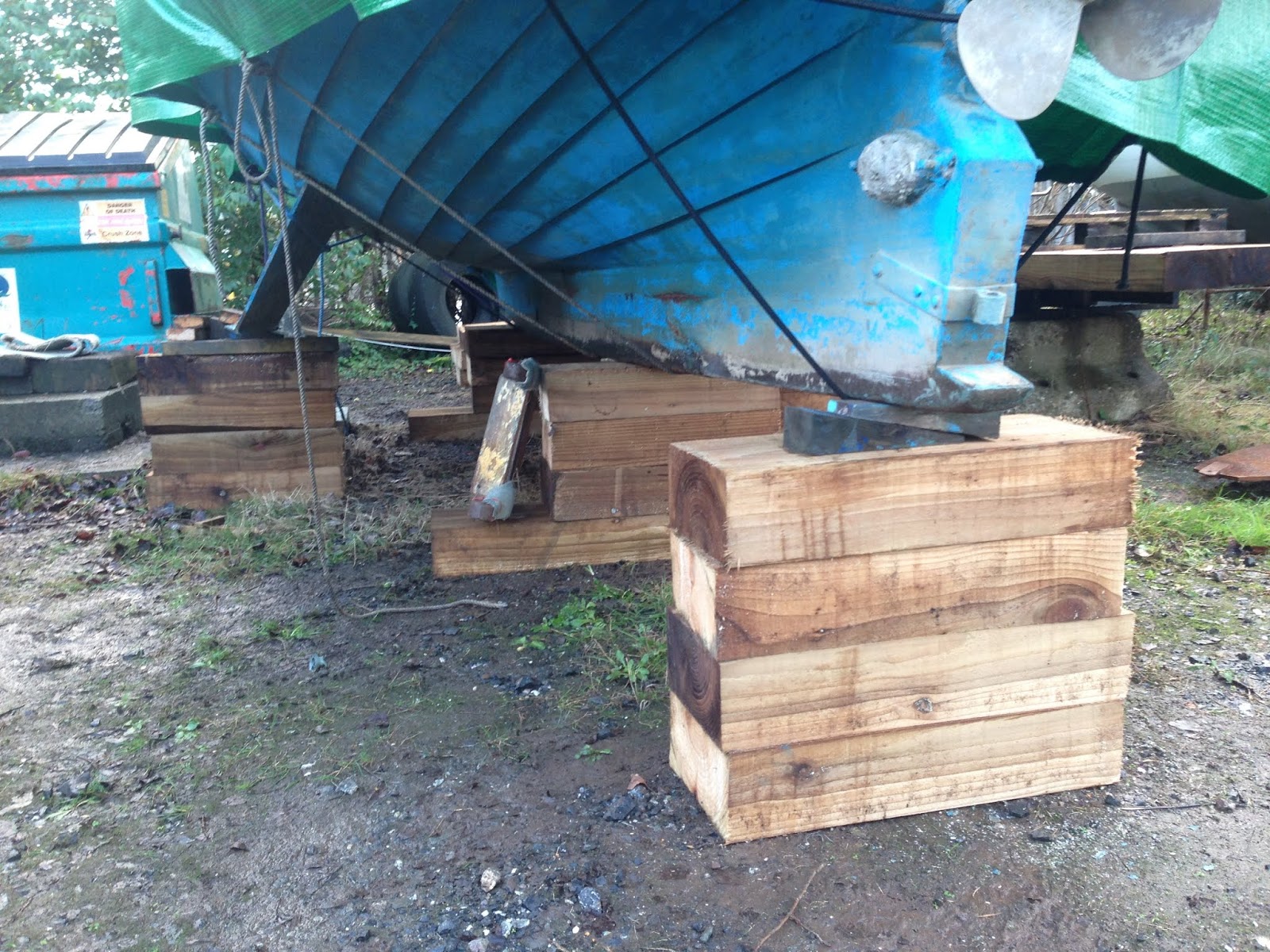
and then set down on blocks high enough to enable the keel bolts to be driven out.
The heads of the nuts of the after two centreline bolts had almost completely dissolved away and their remains were chiselled away and the bolts driven out after the mortar encasing the heads in the ballast keel was broken out. Also removed were the first two forward of the centreboard slot. Their nuts were OK as they are rarely wet compared with the aft ones which are normally submerged in bilge water.
There is one further bolt right at the forward end of the ballast keel but its nut is hidden under the heads and it has been left for now.
All the bolts were intact and the forward ones were still dripping with tar from when they were first installed. The main area of wastage of these was in way of the main timber keel. These centreline bolts are 3/4″ BSW and range in length from 250mm to 290mm. (Going metric for the replacements!)
The next stage was to expose the inboard ends of the keel bolts alongside the centreboard case. There are four of these each side but they are underneath the centreplate case upper part and capping so we had no option but to remove it all. This casing needs attention though as there have been ‘rusty weeps’ seeping in through the lower part for years and this was only going to get worse with time.

A bit of dismantling of the galley unit and the companionway step was required to free the centreplate case sides and they were carefully unfastened. A replacement forward capping had been Sikaflexed and screwed to the forward face at sometime in an attempt to stem the seepage and the Sika sticks so well I had no choice but to chisel the capping to bits to get it off.
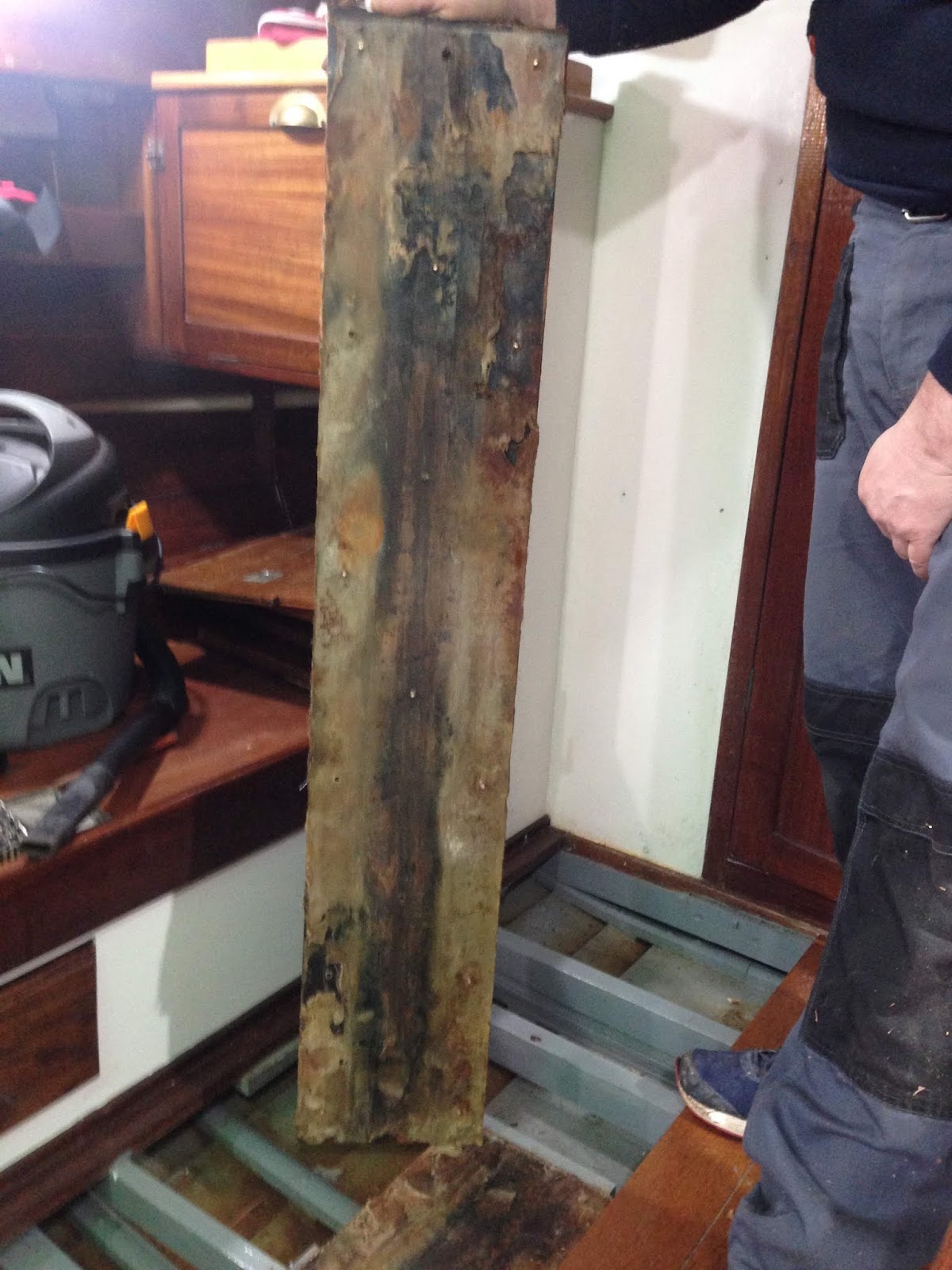
Most of the screws holding the cabin sole capping had to be drilled or broke off but eventually it was free to prise off.

After removing some battens that had been added to the foot of the case and rows of screws and the copper through-fastenings the case sides were freed and removed. The original glue lines had long failed and the step joints were full of mud and crumbling sealant – no wonder she was leaking.

Plugs over the ballast keel bolts were identified and drilled and picked out. We had to take care to identify the ballast bolts as there are others between them which only fasten the centreboard case to the hog/keel and these were not to be disturbed.
The nuts of these bolts were drilled/chiselled away and all but two of these were able to be driven out but put up more of a fight than the centre bolts as they are much longer; up to 420mm. They are (or were when new) 5/8″ diameter.

Two of them refused to give despite a serious beating; one is so wasted it just bent, the other moved a bit but is now solid. We plan to come back to this with a drilling machine to set up over these.

Now that there is nothing much holding the ballast keel on we put a temporary length of M12 threaded rod through two of the holes till the new bolts can be fitted.

All ‘Enfys’ keel bolts came out relatively easily, bar two centre ones that refused to budge. These were seriously wasted and either bent when we tried to drive or the punch slipped off and got jammed. A magnetic base drill was set up over them and we laboriously chewed away at the tops of these until we could get a drive onto the stump and push out the remains of one of the bolts. The other one we heated from below and managed to free it. On both these bolts the holes through the ballast keel were not true and the bolts had been bent when originally installed.
Next: Reassembly.